So, what makes the Synova Laser MicroJet technology so innovative? In 1993, scientists working at the Institute for Applied Optics at the Swiss Federal Institute of Technology in Lausanne, succeeded in creating a water jet-guided laser, referred to as the Laser-MicroJet ® (LMJ) by its inventors. The laser beam is focused into a nozzle while passing through a pressurized water chamber. The geometry of the chamber and nozzle are critical to coupling the energy-rich laser beam in the water jet. The low-pressure water jet emitted from the nozzle guides the laser beam by means of total internal reflection at the transition zone between water and air, in a manner similar to conventional glass fiber optics. The water jet can thus be referred to as a fluid optical wave-guide of variable length. Because a pulsed laser is used, the continuous water jet is able to re-cool the cut immediately, resulting in only a very slight depth of thermal penetration. The results are very narrow, parallel wall, burr-free kerfs, with negligible thermal damage. The water simultaneously washes any contaminants and ablated material away, removing the requirement for any post processing cleaning steps.
Synova Microjet
Synova Laser MicroJet Technology
Synova Microjet
Synova Laser MicroJet Technology
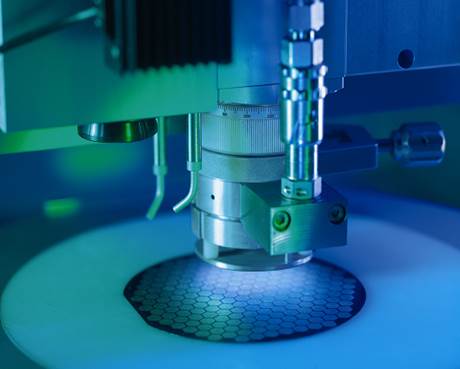
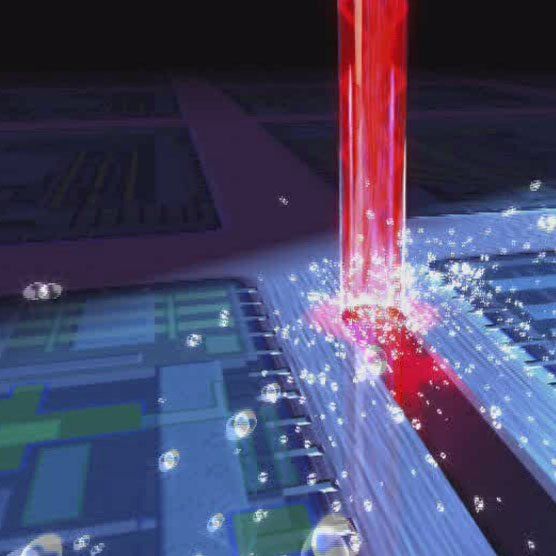
For the first time ever, it is possible to combine the advantages of both water and laser cutting in one operation. Utilizing the difference in the refractive indices of air and water, the technology behind Laser MicroJet® creates a laser beam that is completely reflected at the air-water interface.
The laser is, therefore, entirely contained within the water jet as a cylindrical beam, similar in principle to an optical fiber.
This lack of deviation is maintained through and beyond the work piece, facilitating the accurate cutting of porous or layered materials, all with minimal thermal and structural distortion, leaving a fine cut edge.
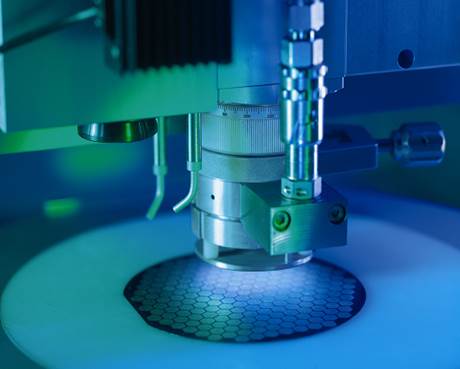
So, what makes the Synova Laser MicroJet technology so innovative? In 1993, scientists working at the Institute for Applied Optics at the Swiss Federal Institute of Technology in Lausanne, succeeded in creating a water jet-guided laser, referred to as the Laser-MicroJet ® (LMJ) by its inventors. The laser beam is focused into a nozzle while passing through a pressurized water chamber. The geometry of the chamber and nozzle are critical to coupling the energy-rich laser beam in the water jet. The low-pressure water jet emitted from the nozzle guides the laser beam by means of total internal reflection at the transition zone between water and air, in a manner similar to conventional glass fiber optics. The water jet can thus be referred to as a fluid optical wave-guide of variable length. Because a pulsed laser is used, the continuous water jet is able to re-cool the cut immediately, resulting in only a very slight depth of thermal penetration. The results are very narrow, parallel wall, burr-free kerfs, with negligible thermal damage. The water simultaneously washes any contaminants and ablated material away, removing the requirement for any post processing cleaning steps.
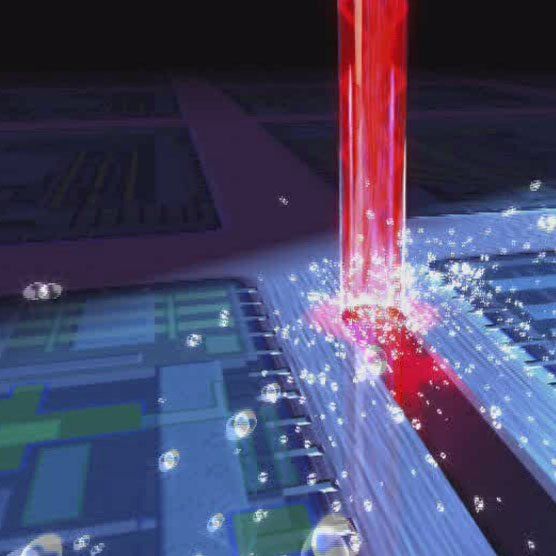
For the first time ever, it is possible to combine the advantages of both water and laser cutting in one operation. Utilizing the difference in the refractive indices of air and water, the technology behind Laser MicroJet® creates a laser beam that is completely reflected at the air-water interface.
The laser is, therefore, entirely contained within the water jet as a cylindrical beam, similar in principle to an optical fiber.
This lack of deviation is maintained through and beyond the work piece, facilitating the accurate cutting of porous or layered materials, all with minimal thermal and structural distortion, leaving a fine cut edge.
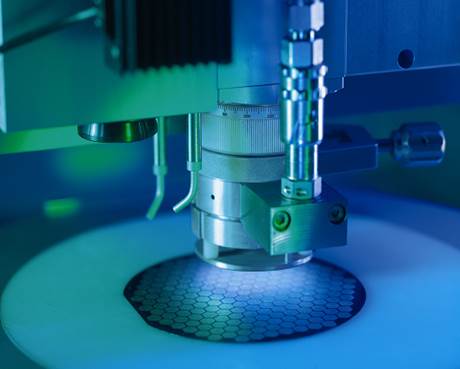
So, what makes the Synova Laser MicroJet technology so innovative? In 1993, scientists working at the Institute for Applied Optics at the Swiss Federal Institute of Technology in Lausanne, succeeded in creating a water jet-guided laser, referred to as the Laser-MicroJet ® (LMJ) by its inventors. The laser beam is focused into a nozzle while passing through a pressurized water chamber. The geometry of the chamber and nozzle are critical to coupling the energy-rich laser beam in the water jet. The low-pressure water jet emitted from the nozzle guides the laser beam by means of total internal reflection at the transition zone between water and air, in a manner similar to conventional glass fiber optics. The water jet can thus be referred to as a fluid optical wave-guide of variable length. Because a pulsed laser is used, the continuous water jet is able to re-cool the cut immediately, resulting in only a very slight depth of thermal penetration. The results are very narrow, parallel wall, burr-free kerfs, with negligible thermal damage. The water simultaneously washes any contaminants and ablated material away, removing the requirement for any post processing cleaning steps.
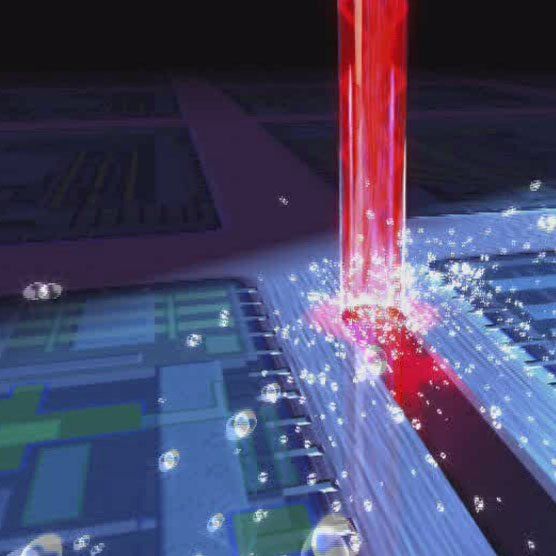
For the first time ever, it is possible to combine the advantages of both water and laser cutting in one operation. Utilizing the difference in the refractive indices of air and water, the technology behind Laser MicroJet® creates a laser beam that is completely reflected at the air-water interface.
The laser is, therefore, entirely contained within the water jet as a cylindrical beam, similar in principle to an optical fiber.
This lack of deviation is maintained through and beyond the work piece, facilitating the accurate cutting of porous or layered materials, all with minimal thermal and structural distortion, leaving a fine cut edge.